The A-Pans
During the production of sugar from sugarcane, there is a pivotal step where the extracted juice starts to solidify into the dry, crystalline product that we find on store shelves. To do this, concentrated sugarcane juice, called syrup, is boiled in batches inside large tanks where it ultimately crystallises. These tanks are called “pans”. Multiple pans are used in the crystallisation process, of which the first set is called the A-pans.
Operation of the A-pans is a complex batch process. The process and naming conventions differ slightly depending on the specific infrastructure and preferences at each mill; one example will be described here, as it relates to a prominent South African sugar mill.
To start, syrup enters an A-pan along with magma - a slurry of fine crystals which kickstarts the crystal formation process. At this particular mill, this first batch of a cycle is called the 4A boil. The pan is boiled, and sugar starts to crystallise. Once these crystals have sufficiently grown in size, the pan is divided (“cut”) by transferring half its volume into another pan so that crystal growth can continue. The contents of the 4A boil that have been cut in half are now referred to as 2A boils. Similarly, when sugar crystals in these two pans reach a certain size, these pans are cut as well. This results in four pans (the 1A boils), which boil and crystallise further until all this sugar can be transferred to, and collected in a large receiving tank. This final action is called a “strike”. From here, the sugar process continues through further pans and centrifuges until the final product is obtained.
.png)
On paper, this seems simple enough. However, many complications need to be considered:
- At this particular mill there are a total of 6 physical pans in the A-pan section (Not 7 as per the above process schematic). Accordingly, once the 4A is cut, half is transferred to a new 2A pan, whilst half remains in what is then considered the 2nd 2A pan.
- Once a pan is emptied, another crystallisation cycle (4A to 2A to 1A) can be initiated with magma. More than one cycle of crystallisation therefore runs simultaneously in order to use the available pans optimally.
- When these 6 pans operate concurrently, clashes between cycles can easily occur. For example, a pan may need to be cut, without an empty pan being available.
- Pans containing a 4A generally boil for 2.5 hours, while other pans need only boil for about 1.5 hours. However, we found that these times can vary depending on the pressure in the vessel, the state of pan maintenance, etc.
- A pan can be made to boil longer when it needs to wait for space to become available by adding more water; however, this is extremely inefficient in terms of steam consumption.
- At this mill there are a further 4 storage vessels available that can temporarily hold sugar if there are no open pans available; however, these are limited and using them wastes steam.
- Certain pans are preferred for certain actions due to their position on the factory floor, or due to their boiling times being slower or faster than normal.
- Only two actions can be performed at a time, e.g., you cannot make three cuts at the same time.
- During plant instability, e.g. when cane feed supply is inconsistent, the amount of syrup available can vary significantly.
- Additionally, each pan operator has their own preferred method of scheduling the pans, resulting in varying processes and efficiencies per shift.
- Moreover, due to the crystallisation cycle being lengthy and complex, batch processes regularly span operator shifts. Consequently, differing scheduling and operational methodologies applied by different shift operators induce complexities and inefficiencies both in shift hand-over procedures, as well as hours thereafter when the current operator misinterprets information, scheduling decisions, or operational actions from the previous shift.
- All of the above must also be contemplated within the framework of the wider and highly complex sugar production process, where interruptions, irregularities and anomalous events are regular occurrences – certain of which may materially impact on the crystallisation cycle and its efficient management.
Correctly timing cuts, strikes, and the initiation of new crystallisation cycles, is therefore a highly intricate process, that is currently being controlled by a single operator at a time and without intelligent and process-responsive tools available to enable stable operational cadence.
Optimisation Objectives
Nanodyn’s primary objective was to create increased value from the A-Pans at a particular sugar mill in South Africa, by creating a smart scheduling algorithm.
More specifically, we aimed to:
- prevent scheduling conflicts in the batch processes;
- reduce the steam waste caused by boiling a pan with additional water;
- reduce the need for operator improvisation during standard operations;
- increase throughput by maximising batch completions (i.e., strike rate); and
- allow smooth plant operation by ensuring that the smart algorithm is responsive to anomalous process events or operator actions.
Our solution: The A-Pan Scheduler
The A-Pan Scheduler is an Advanced Process Control model that intelligently schedules operations in the A-Pans of a sugar mill. The model fully integrates with DCS data from the mill to calculate possible future events in the pan packing process. The model then uses this data to suggest which actions to take.
The scheduling algorithm has been set up to consider all the complexities of the A-Pan packing process. The algorithm adheres to operational constraints and keeps track of events, such as cuts and strikes. It considers the availability of pans and storage vessels, now and in the future. It also considers the amount of syrup available and schedules events such that syrup is available when needed. Other anomalies are also taken into account, such as unplanned events, mistakes, and our discovery that specific pans are more suitable for starting a new cycle than receiving a cut batch.
To enable use of the schedule, and assist plant operators with their decision making, a visual output is generated. As soon as an action is taken, as suggested or otherwise, the model adapts and recalibrates to suggest the best subsequent action. If a pan boils longer than anticipated, the model will also recalibrate and reschedule. The following visualisations are generated:
- Pan Packing Schedule: An online predictive queue which details a list of required actions and the time at which each is recommended to occur.
- Pan Magma Schedule: A timer which indicates exactly when magma should be initiated, i.e. when a new 4A boil should start. This is helpful to anticipate and plan in advance.
- Pan Packing Event History: A log of all operations and events that have occurred.
- Pan Packing Performance History: A bar graph presenting summary statistics for the events that have taken place.
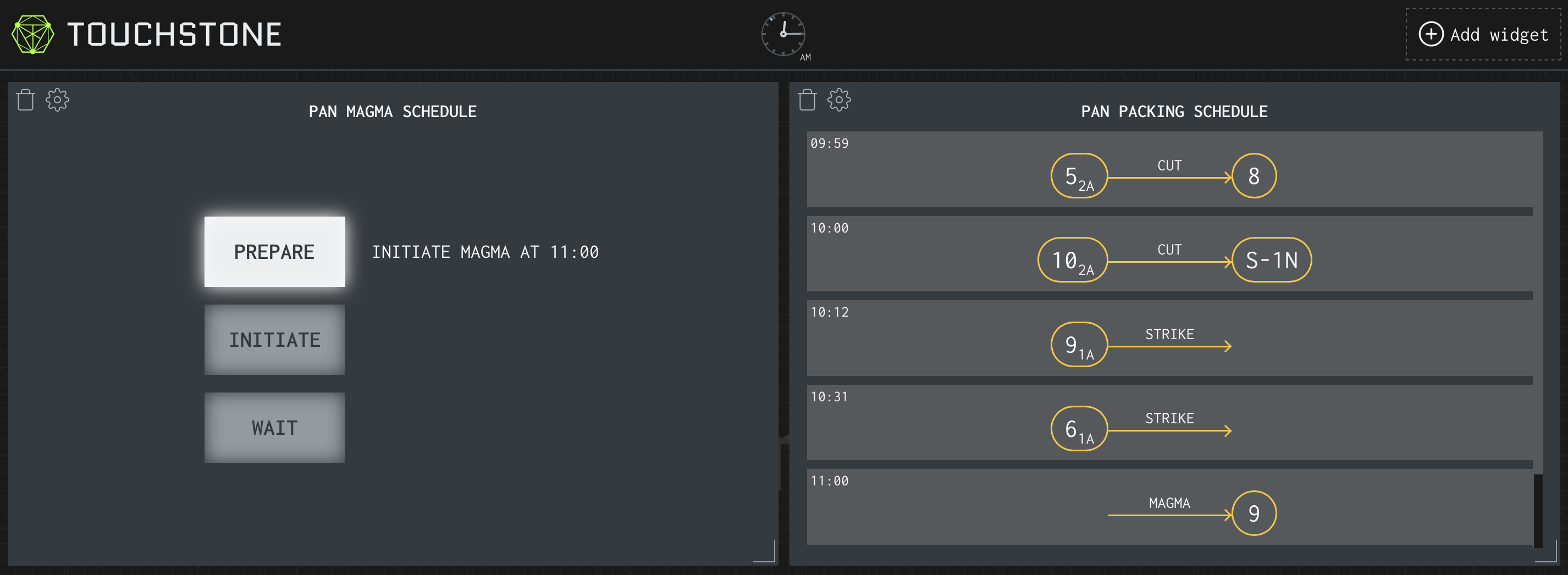
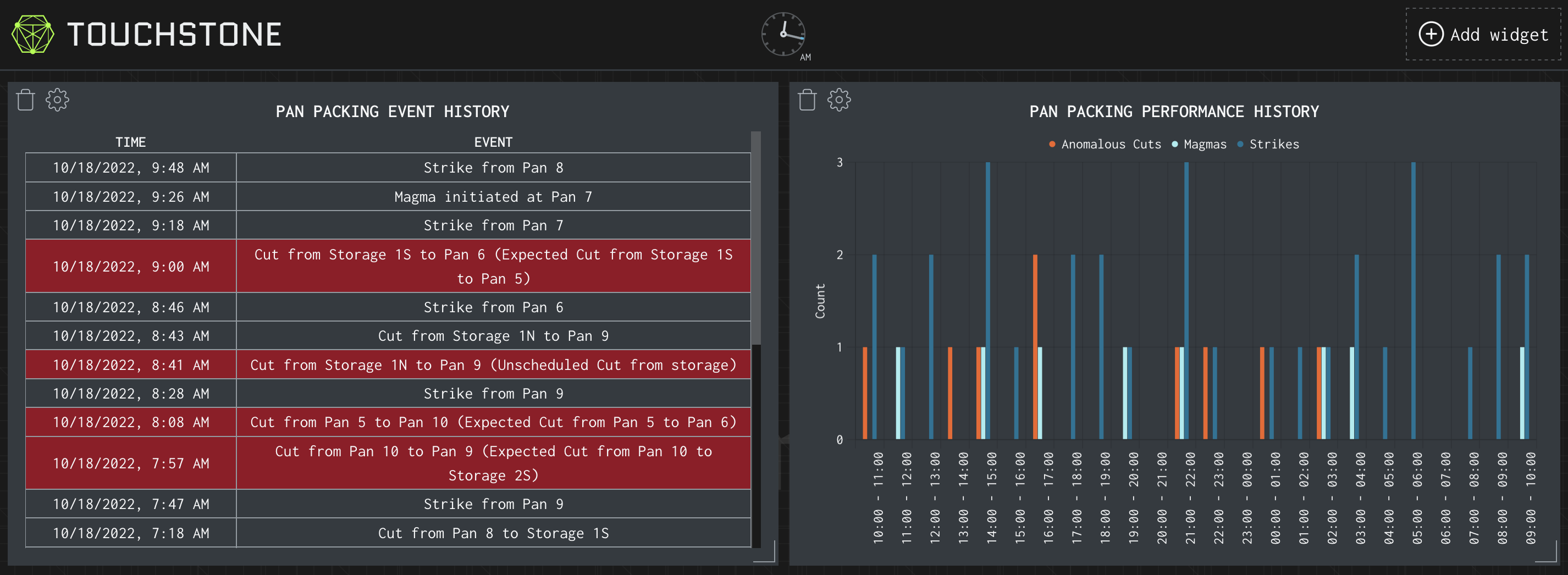
Impact of the A-Pan Scheduler: On Energy Consumption
Adoption of the A-Pan Scheduler and adherence to its instructions will reduce scheduling conflicts in the A-Pans. In turn, this will decrease the occurrence of instances where pans need to be kept boiling with additional water while waiting for another vessel to open so that it can be cut to it. This waiting period is an unnecessary waste of steam and energy. Over the course of a production season, the amount of steam and energy wastefully expended in this process are material – 10% or more. The schedule will mitigate this waste.
Additionally, upon adoption of the A-Pan Scheduler at this particular mill, an increase in batch completions was observed (a higher strike rate), along with a higher production consistency amid plant irregularities, leading to a more predictable output for downstream processes. More predictable processes can be run more energy efficiently, and contribute to an optimised plant-wide energy and flow balancing.
Impact of the A-Pan Scheduler: On Operator Decision Making
Adoption of the A-Pan Scheduler will aid operators in their decision making. Adherence to the schedule prevents uncertainties and schedule-clashes, which are difficult to solve. Use of the scheduler also facilitates and simplifies shift changes and handovers between different operators, who currently often follow different operating procedures. Additionally, there is a high risk of rash decision making during times of intense factory turbulence, such as when syrup flow fluctuates excessively; this potential for error can be mitigated entirely.
Impact of the A-Pan Scheduler: On Management Decision Making
Deployment of the A-Pan Scheduler allowed us to carry out extensive statistical analyses regarding factory operations, mass balance, as well as water and power consumption. These analyses allowed us to detect additional losses in efficiency. For example, pressure control issues, pan performance decay, syrup or steam flow control problems, errors in sensor calibration, operational inconsistencies between shifts, etc.
Adoption of the A-Pan Scheduler thus aids management in monitoring mill operations, identifying problem areas, and scheduling maintenance. A graphic representation of daily pan state and boiling lengths is generated for this purpose, providing management with an accessible and interpretable view of daily operations on the A-Pan floor.
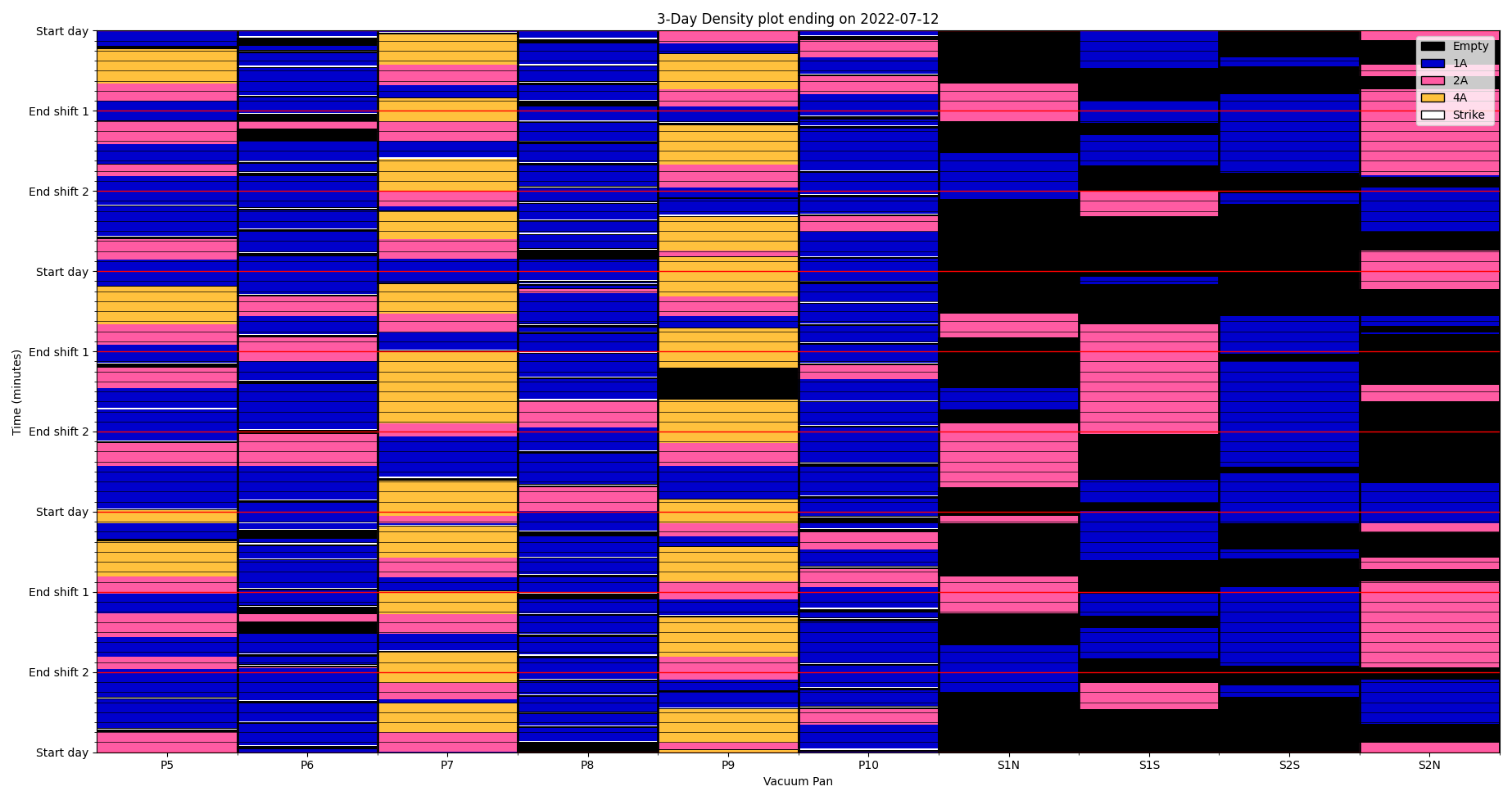
Dr. Jean Lombard (PhD Chemistry), Programme Manager at Nanodyn