Brix Measurement in Sugar Mills
Sugar production involves a series of complex processes that transform sugar cane into various products, including granulated sugar, powdered sugar, and molasses. During this process, sugar is extracted from sugar cane as juice, which is then concentrated into syrup, crystallised, and refined into the final sugar products.
Brix measurement plays a vital role in sugar production, as it is used to determine the sugar content in juice and syrup. For a 100-gram juice sample, 1 degree Brix indicates that there is approximately 1 gram of sucrose in the solution. To achieve a maximum sugar yield, a specific Brix level must be attained at each step of the production process. For example, a particular Brix level is required for the crystallisation step to yield discrete sugar crystals of the right size. Additionally, monitoring Brix levels can help identify potential issues in the production process, such as equipment failure or inconsistencies in the sugar cane itself.
Unfortunately, online Brix meters are expensive instruments, and sugar mills rarely possess more than one or two units. Furthermore, because Brix meters are important instruments, they require disciplined oversight to ensure they are both functional and calibrated. Nanodyn has regularly found such instruments to output incorrect data, unbeknownst to the relevant responsible technicians and process experts. To make up for the lack of sensors, Brix measurements are sometimes taken offline in a laboratory, but this causes significant delays in obtaining the data, and thus cannot be used for real-time process optimisation.
The Evaporator Cascade
During the sugar production process, there is a pivotal step where the extracted sugar cane juice is concentrated in a multiple-effect evaporator cascade.
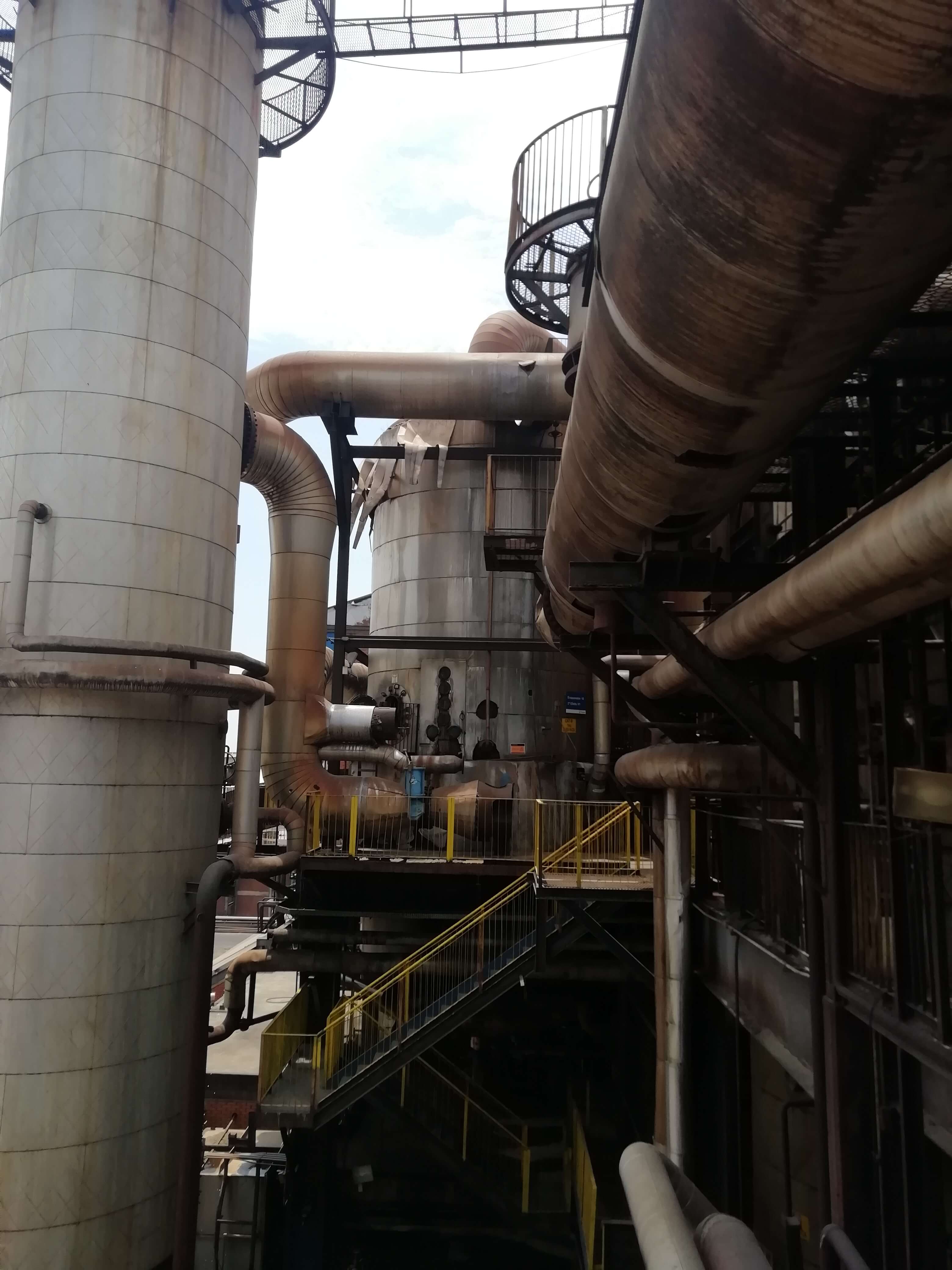
In a typical mill, several effects are used, each containing a number of evaporators that are heated using steam. Inside each evaporator, there are thousands of tubes through which the juice passes, allowing water in the juice to evaporate. As the juice becomes more concentrated and turns into syrup, the Brix value increases.
Monitoring Brix values throughout the evaporator cascade will indicate whether sufficient evaporation is occurring, or whether there are any issues that need attention. The steam flow to the evaporators as well as the amount of vacuum applied must be carefully controlled. Additionally, the evaporator tubes foul up over time, which reduces heat transfer and thus evaporation. These issues should be monitored closely.
The Problem
A leading Brazilian sugar mill aims to increase throughput at their evaporator cascade. However, they currently have no way of determining the Brix values between their five effects. Brix is only measured at the inlet and outlet of their evaporator cascade, which leads to a black-box effect and provides no indication of where problems may be arising
Our Solution: The Virtual Brix Sensors
Nanodyn has created a set of five Virtual Brix Sensors to equip the mill with intermediate Brix values at points in the evaporator cascade where no real-world Brix sensors are located.
The Virtual Brix Sensor is a mathematical model based on general chemical engineering and analytical heat and mass transfer principles. The model infers Brix values in the absence of physical Brix sensors through a mass-balance simulation of the plant which combines information from multiple other sensors.
The model is therefore based on first principles and regressed onto data from real sensors in the plant. Instantaneous Brix is calculated using live plant data, eliminating the need for large persistent simulations. This enables the model to operate in situations of alternating evaporator cleaning and shutdown.
The Virtual Brix Sensors thus provide Brix values at a number of points in the evaporator cascade, in real time. This equips the mill so that they are able to investigate and intervene in their process. The virtual Brix values are displayed on Nanodyn’s proprietary web based interface, Touchstone (below).
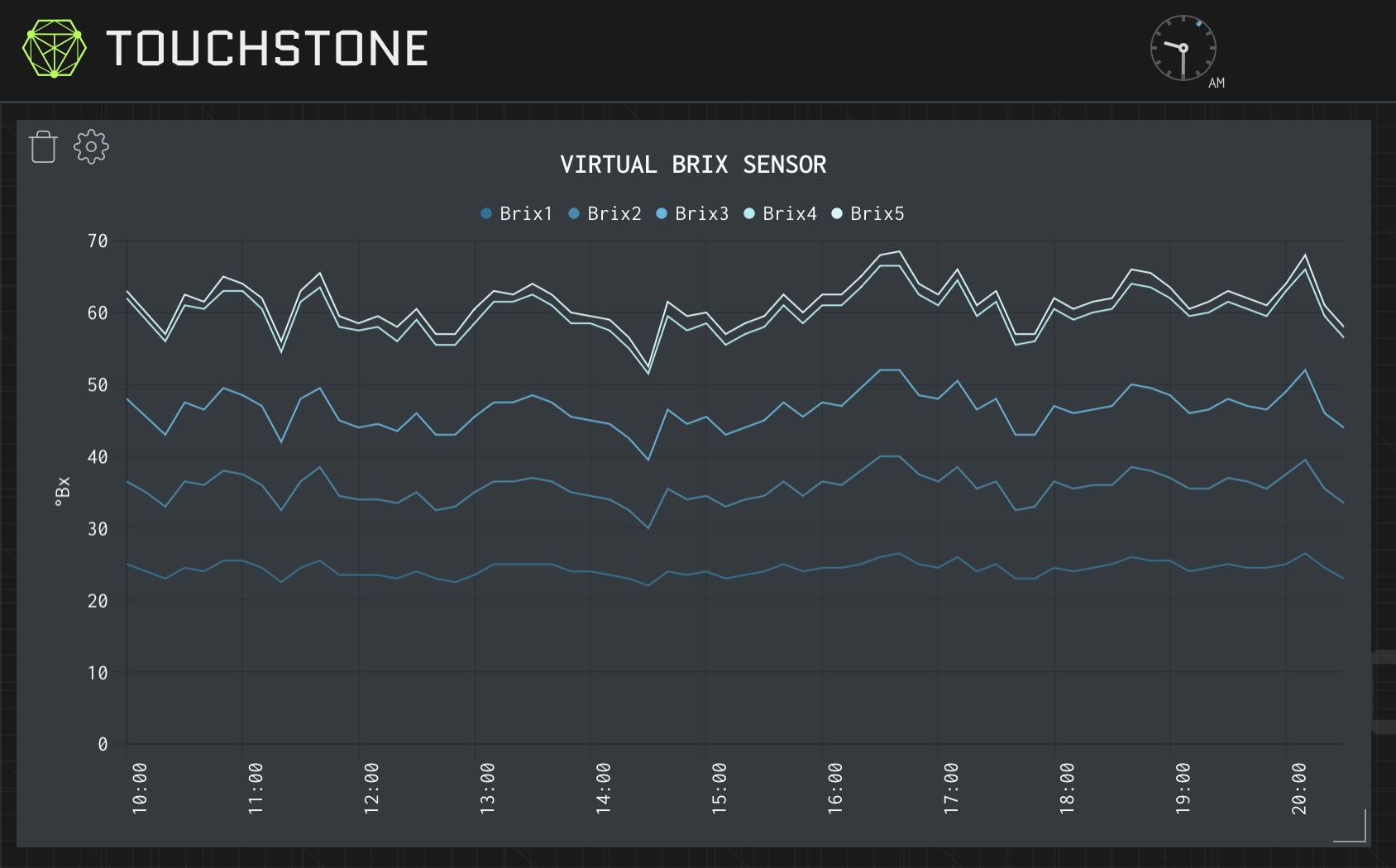
The Value of Virtual Sensors
Virtual sensors are becoming increasingly valuable in industry, particularly in situations where it is difficult or expensive to install physical sensors. By using mathematical models and combining data from multiple sensors, virtual sensors can infer important parameters and provide real-time monitoring and control. This allows for more efficient and effective operation of industrial processes, as well as early detection and prevention of issues. Virtual sensors can also provide more visibility into plant operations, allowing for better decision-making and optimisation.
At this particular mill, the virtual Brix sensors provide deeper insight into plant operations and inform mill operators of anomalies and performance fluctuations. Moreover, this is all achieved at a fraction of the cost of installing the equivalent physical Brix sensors.
Dr. Jean Lombard (PhD Chemistry), Programme Manager at Nanodyn