Filtration in a sugar refinery
Raw sugar extracted from sugar cane has a distinct brown colour. The removal of colour, and other impurities, from this raw sugar is an important step in the production of refined, table sugar. In a sugar refinery, there are several ways that colour can be removed from sugar. One common colour-removal method is filtration, specifically cake filtration.
To carry out cake filtration, the raw sugar first has to be melted to form a syrup that can easily flow through a filter. A filter medium is then added, which forms an insoluble suspension that is captured on the filter as a filter cake. When the syrup passes through this filter cake, both the colour molecules and the filter medium stay behind and are incorporated into the cake as it continues to form. This causes the cake to increase in mass. As the cake grows, the resistance to flow increases and a throttling valve must be used to maintain the flow rate. When the cake reaches a critical point the flow can no longer be maintained and the filter ideally needs to be cleaned.
Cleaning a filter can take about 30 minutes, but thereafter it can take another 20 minutes before the filter cake has sufficiently built up again, to maintain the flow and efficiently remove colour. The syrup that passes through the filter during this time will need to be filtered again (i.e. recycled) to remove all the colour. Cleaning a filter is therefore time-consuming, and several factors need to be considered:
- If filters are cleaned too frequently, losses will occur due to operational downtime and an increase in the amount of syrup that needs to be recycled.
- However, a dirty filter will have a low flow which severely decreases refinery throughput.
- Inconsistent flow can also lead to holes in the filter cake (called “breakthrough”), in which case the syrup will need to be recycled.
- Additionally, there are a number of filters that make up a filter bank in a refinery, but cleaning too many simultaneously leads to compounding recycle rates.
- A filter bank also often contains different types of filters, each of which can be used for different lengths of time before they need to be cleaned.
Performance optimisation objectives
A well-known sugar mill in South Africa has an operational bottleneck at its refinery filters. Raw sugar from a number of sugar mills in the area is processed at this refinery; therefore, a large throughput capacity is essential to keep up with the demand for refined sugar.
Nanodyn’s primary objective was to alleviate this operational bottleneck by increasing the refinery throughput by means of maximising the flow through the filters, specifically, through clean filters.
To do this, we aimed to determine the optimal cleaning schedule for the refinery’s eight filters, and to orchestrate the cleaning such that the filters can be cleaned on time, preventing decreases in flow and the potential for filter breakthrough.
Our solution: The Refinery Filter Scheduler
The Refinery Filter Scheduler (RFS) is an advanced process control scheduling algorithm for the optimisation of refinery filter cleaning.
The RFS fully integrates with refinery DCS data and has been optimised to consider all operational constraints at the sugar mill in question. The model considers pressure, flow, and volume readings as input variables, and assesses the relationships between these variables during operation, to predict the fouled state and efficiency of each individual filter, now and in the future.
The RFS can therefore predict the productive time remaining for each filter before cleaning is necessary. Given that only one filter should be cleaned at a time, a schedule is created to allow for sufficient time to clean each filter sequentially, before they reach a critical state of fouling. Thus maximising volumetric throughput in the refinery.
Absolute adherence to the schedule by refinery operators when there is sufficient feed should lead to:
- Filters being used for as long as possible before cleaning;
- Thus increasing throughput;
- Without the risk of fouling filters too much, and creating a bottleneck of too many filters that need to be cleaned at the same time;
- In addition, high reject volumes due to cake breakthroughs (which need to be recycled) could be avoided.
The schedule generated by the RFS indicates the time at which each filter should be cleaned, with overdue, critical cleans being highlighted for attention. The schedule is updated every 5 minutes and displayed on Nanodyn’s proprietary web-based user interface, called Touchstone.
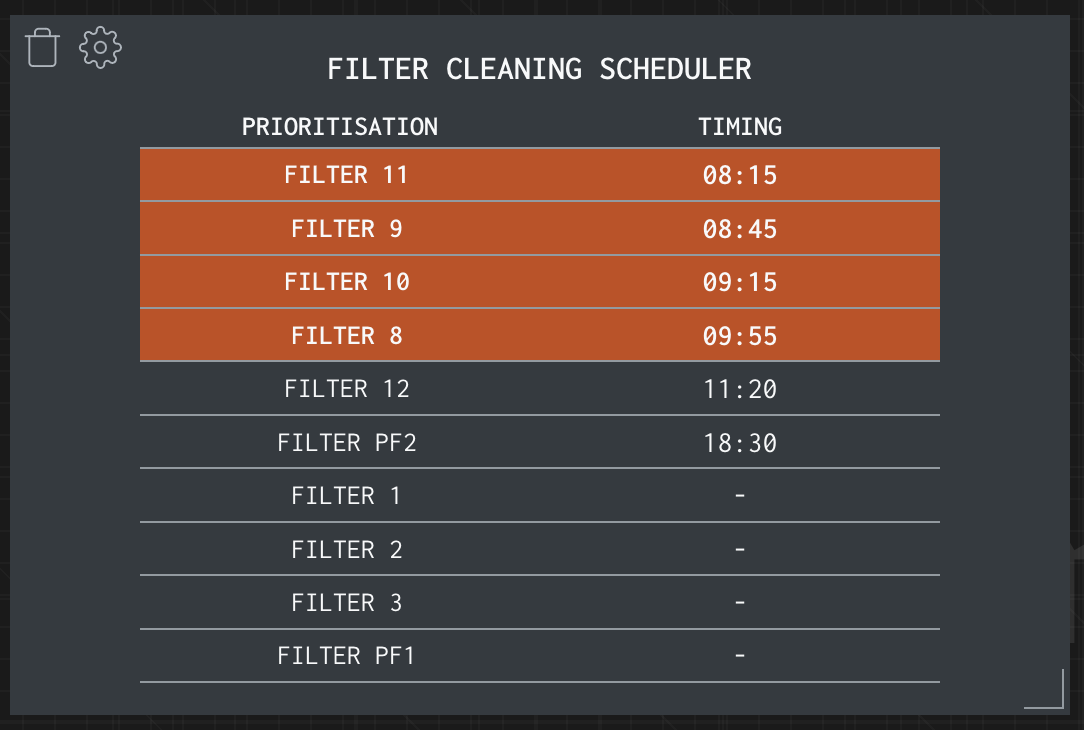
More details regarding technical aspects of the RFS can be found in the following peer-reviewed, published conference paper: O’Kennedy, S. J., Bertossi, L., and Smith, S. (2022). “Real-Time Data Driven Maximisation of Filter Bank Throughput”, SASTA Annual Congress 2022, Durban, 16 18 August.
Technical Performance of the RFS
The RFS was implemented at a prominent sugar refinery in 2022. During this time, model performance was monitored and validated. On average, given adherence to the schedule and sufficient feed supply, the flow through the refinery’s filters increased after adoption of the scheduler. This resulted in:
• An increase of ~457 m3 per day across all eight filters; which equates to
• An increase in average daily production of refined sugar by 308 tonnes;
• Which means that there was a more than 25% increase in daily production when compared to historical refinery performance over the course of three production seasons.
Impact of the RFS on operator decision making
The RFS provides plant operators with a simplified scheduling table that is easy to follow. Adherence to the RFS scheduling guidelines helps operators to make more informed decisions about allocating valuable time and resources to filter cleaning and maintenance.
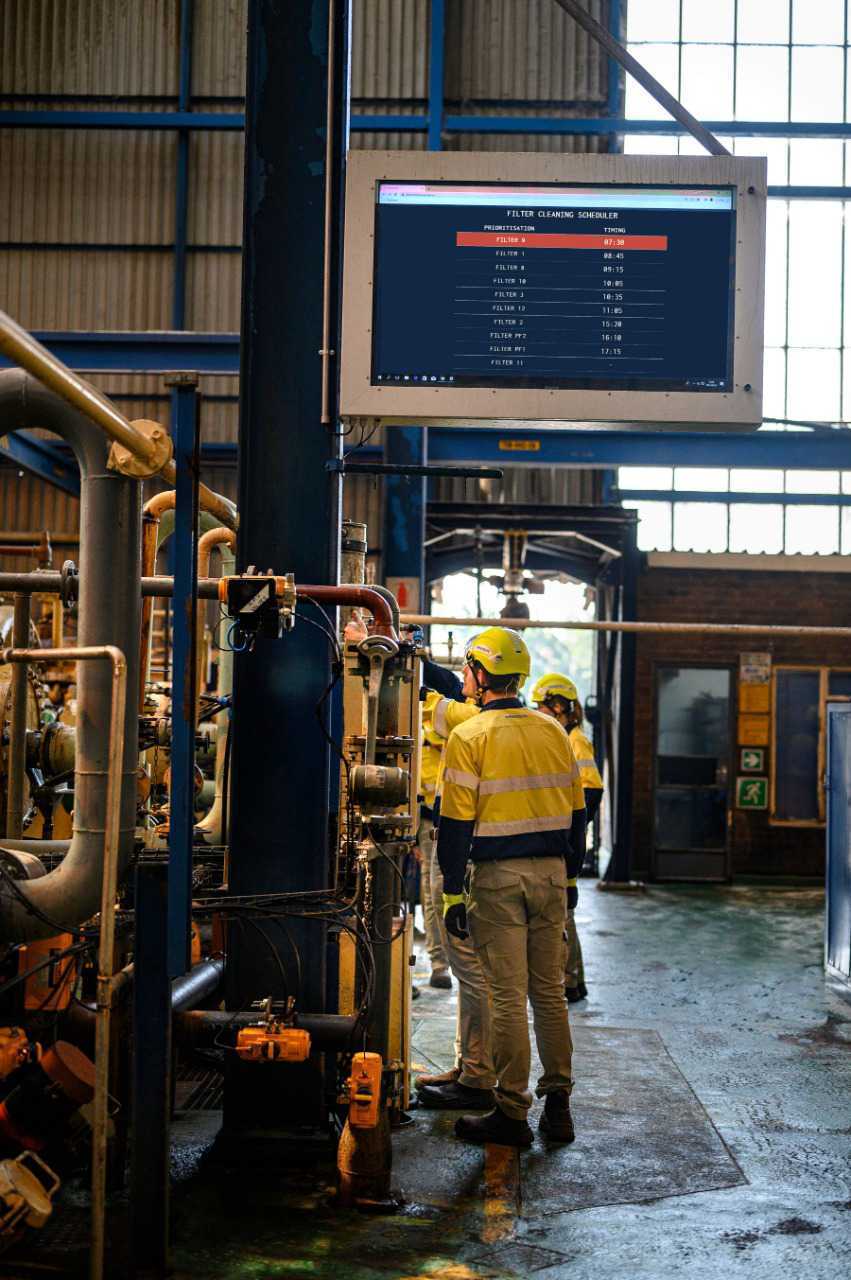
Impact of the RFS on management decision making
A visualisation of the Filter Performance History is also provided by the RFS in addition to the cleaning schedule. The Filter Performance History provides a historical account of the operational efficiency of each filter over the last 24 hours. It indicates when filters are running optimally, how long they are being run with a decreased flow, i.e. overdue for cleaning, and how long the filters are offline for cleaning.
In the figure below, each horizontal line represents the operation of a filter. The blue segments represent the filter operating under healthy flow conditions and the orange segments indicate when the filter was operating beyond its optimal parameters.
Management can thus easily track the performance of their filters.
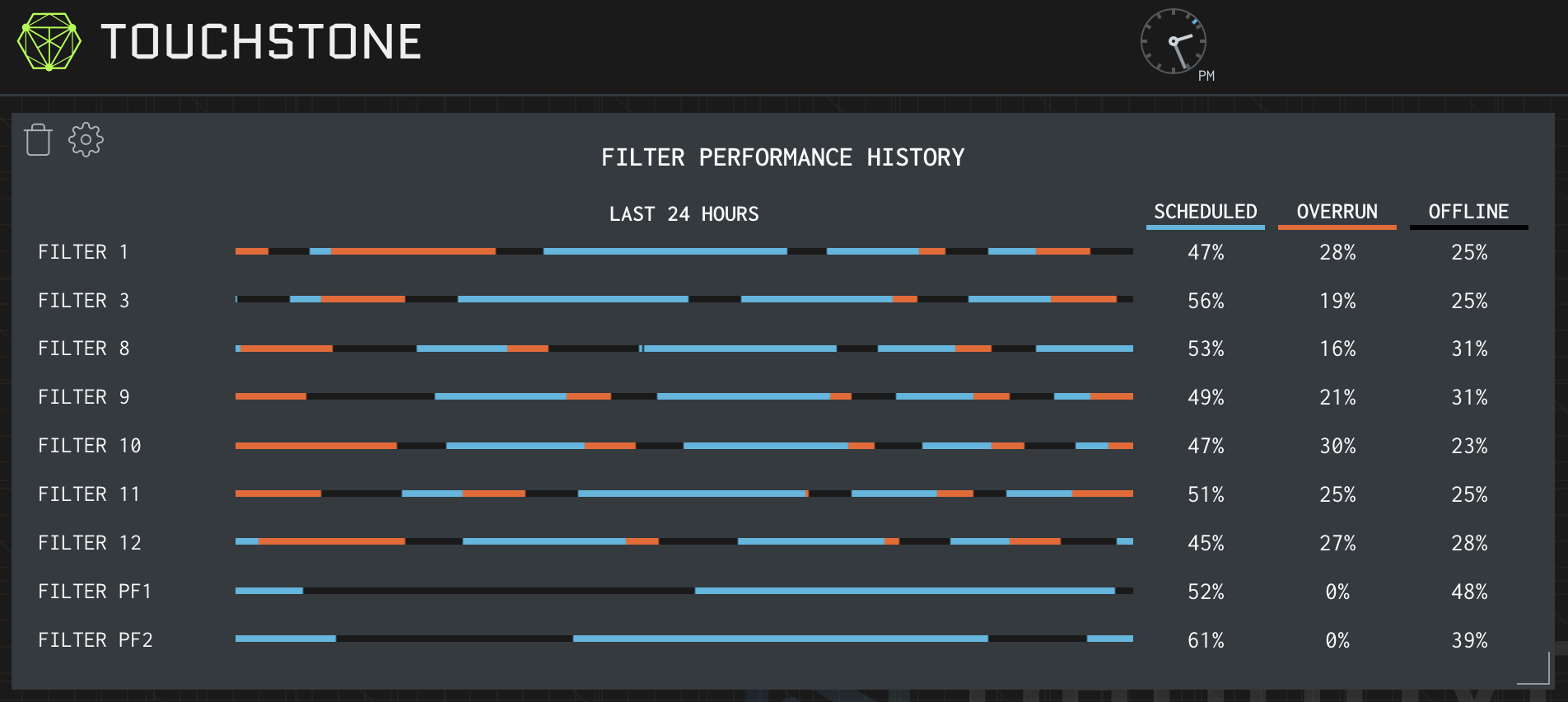
Financial value of the RFS
Adoption of the RFS is of immense value to the refinery as a higher average daily production of refined sugar naturally leads to additional profit. More specifically:
- For the 86 consecutive production days following RFS integration, the Mill generated ZAR 13.24 Million in additional profit above the expected performance trend;
- For the 25 consecutive production days following the integration of the RFS, the Mill generated ZAR 3.8 Million in additional profit in excess of the equivalent production period in 2021; and
- For the 86 consecutive production days following the integration of the RFS, the Mill generated ZAR 14.59 Million in additional profit in excess of the equivalent production period in 2020.
Presentation of these results at the South African Sugar Technologists’ Association’s annual congress was awarded the coveted Cecil-Renaud Factory Prize for the best paper by authors not part of a scientific or technological institute.
Dr. Jean Lombard (PhD Chemistry), Programme Manager at Nanodyn